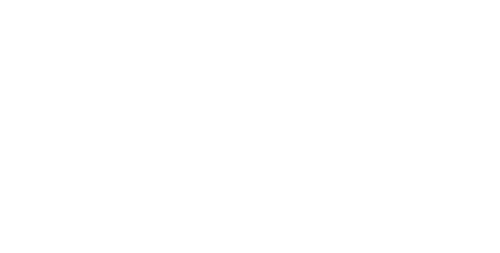
Stillstandszeiten minimieren
Druckluftbehälterprüfung
mit Schallemission
Korrision, Risse oder Leckagen an Druckluftbehältern sind für Betreiber von Pharma-Produktionsanlagen ein ernsthaftes Risiko. Entscheidend ist, drohende Schäden frühzeitig und zuverlässig zu erkennen, um rechtzeitig gegenzusteuern. TÜV SÜD zeigt, wie das mit Hilfe der Schallemissionsprüfung gelingt und gleichzeitig für reduzierte Stillstandszeiten sowie die geforderte Druckluftreinheit sorgt.
Alternative Prüfmethoden
Nach BetrSichV dürfen bei Druckgeräten alternative Prüfmethoden auf Basis von Prüfkonzepten eingesetzt werden. Dazu zählt auch die SEP als Zerstörungsfreies Prüfverfahren (ZfP). Voraussetzung ist ein von einer Zugelassenen Überwachungsstelle (ZÜS) bestätigtes Prüfkonzept des Arbeitgebers, das bezogen auf die Anlagensicherheit gleichwertige Aussagen liefert wie traditionelle Prüfungen. Auf Basis eines solchen Konzepts können Anlagenkomponenten mit ZfP kontrolliert werden, ohne dass sie außer Betrieb zu setzen sind. Gemäß Prüfkonzept kann eine SEP sogar die Innenbesichtigung des Druckgeräts im Rahmen der inneren Prüfung ersetzen.
Sensoren und Prüfdruck
Um die SEP durchführen zu können, sind vor der Prüfung piezoelektrische Sensoren an der Behälterwand zu befestigen. Bei Druckgeräten aus ferromagnetischen Werkstoffen werden Magnethalter eingesetzt. Zwischen dem Sensor und der metallischen Oberfläche des Behälters wird Koppelpaste verwendet, um eine korrekte Verbindung für die Wellenübertragung zu erhalten. Voraussetzung für eine SEP ist die Druckaufbringung während der Messung. Deshalb wird das Druckgerät mit einem stetig steigenden Druck beaufschlagt und dabei mit den Sensoren überwacht. Der Prüfdruck PTSEP sollte so eingestellt werden, dass er mindestens das 1,1-fache des maximal im laufenden Betrieb auftretenden Betriebsdrucks POP beträgt. Dieser Wert gilt für eine Gasdruckprüfung mittels SEP als Ersatz der Innenbesichtigung bei der inneren Prüfung.
Schallwellen
Gibt es aktive Fehler im Werkstoff, wie zum Beispiel Risse, so werden diese durch die Druckerhöhung zum Wachstum – zur sogenannten Rissuferreibung – angeregt. Im Gefüge des Werkstoffs wird damit ein mechanischer Bewegungssprung erzeugt, der seine Umgebung anstößt. Diese gibt elastisch nach und federt zurück, was eine transiente elastische Schallwelle auslöst, die sich von ihrer Quelle ausgehend ausbreitet und von den Sensoren aufgenommen wird. Der Piezokristall des Sensors wandelt die mechanischen Wellen in elektrische Signale. Diese werden mit einem Prüfrechner aufgezeichnet, in einem digitalen Zwilling grafisch dargestellt und von erfahrenen Prüfingenieuren interpretiert und bewertet. So lassen sich Veränderungen im Gefüge des Werkstoffs detektieren, bevor es zu kritischen Zuständen kommen kann. Häufig sind viel genauere Aussagen als bei den traditionellen Sicht- oder Druckprüfungen möglich. Das gilt auch für die Beurteilung von unkritischen Inhomogenitäten oder Mikrorissen, die im Betrieb nicht weiterwachsen und deshalb belassen werden können.